Robin the Eyeshadow Palette is an independent product design, aiming to explore a “twisting” operation logic that simplifies the process of opening an eyeshadow palette. The powder containers are interchangeable, so users could only buy the colors they need, instead of replacing the whole box, which is more sustainable. The digital mockup was built in Blender and rendered in KeyShot, while the physical prototype was 3D printed by resin. During the process, I gained modeling and testing skills, and learned how to finish 3D-printed components with sandpaper and spray paints.
Dimension: 75mm x 75mm x 30mm
Photo documentations
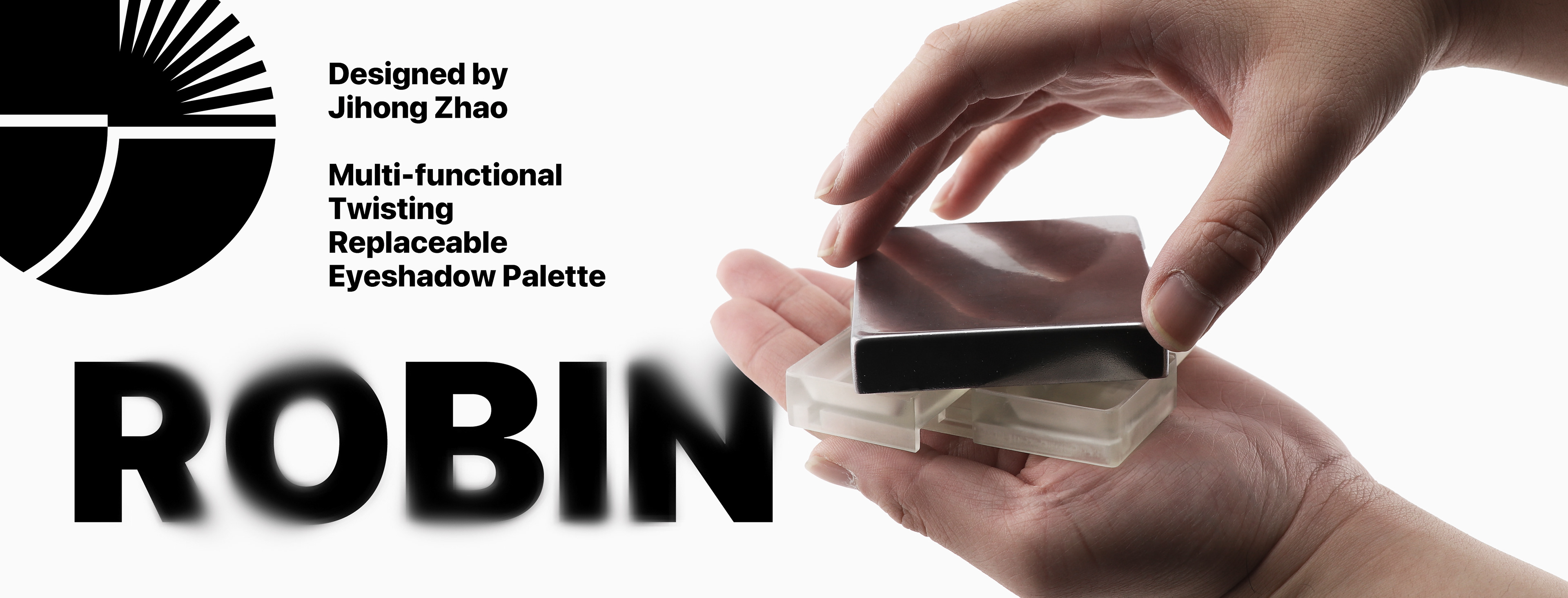
Renderings
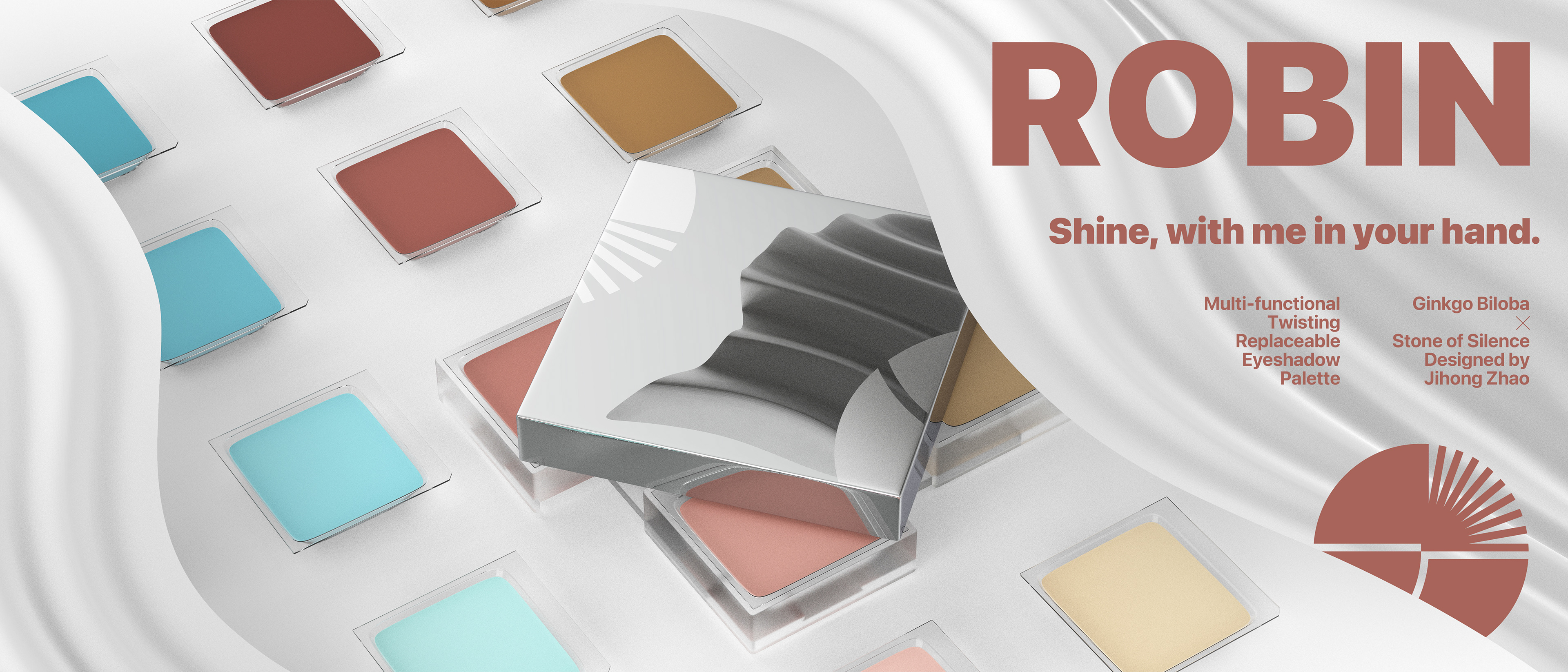

Problem Statement
The current operation logic of makeup products like eyeshadow palettes from mainstream brands is limited to pulling, twisting, and opening a hinge-like structure. This is a decent operation in most cases but could be improved in certain circumstances because both hands are needed to complete the operation, even if the box is placed on a flat surface.
According to observation, more people with makeup needs tend to simplify the process of putting on their makeup, because a traditional makeup process is long and tedious. If the users simply want one layer of powder and eyeshadow, carrying the whole set of makeup is not necessary. Some people potentially want to try makeup but worry about the complex process and confusing choices in the market.
Therefore, I want to create an easy-to-use makeup vessel that involves "twisting" as the main operation logic, so users can easily open it with one hand when it is placed on a flat surface.
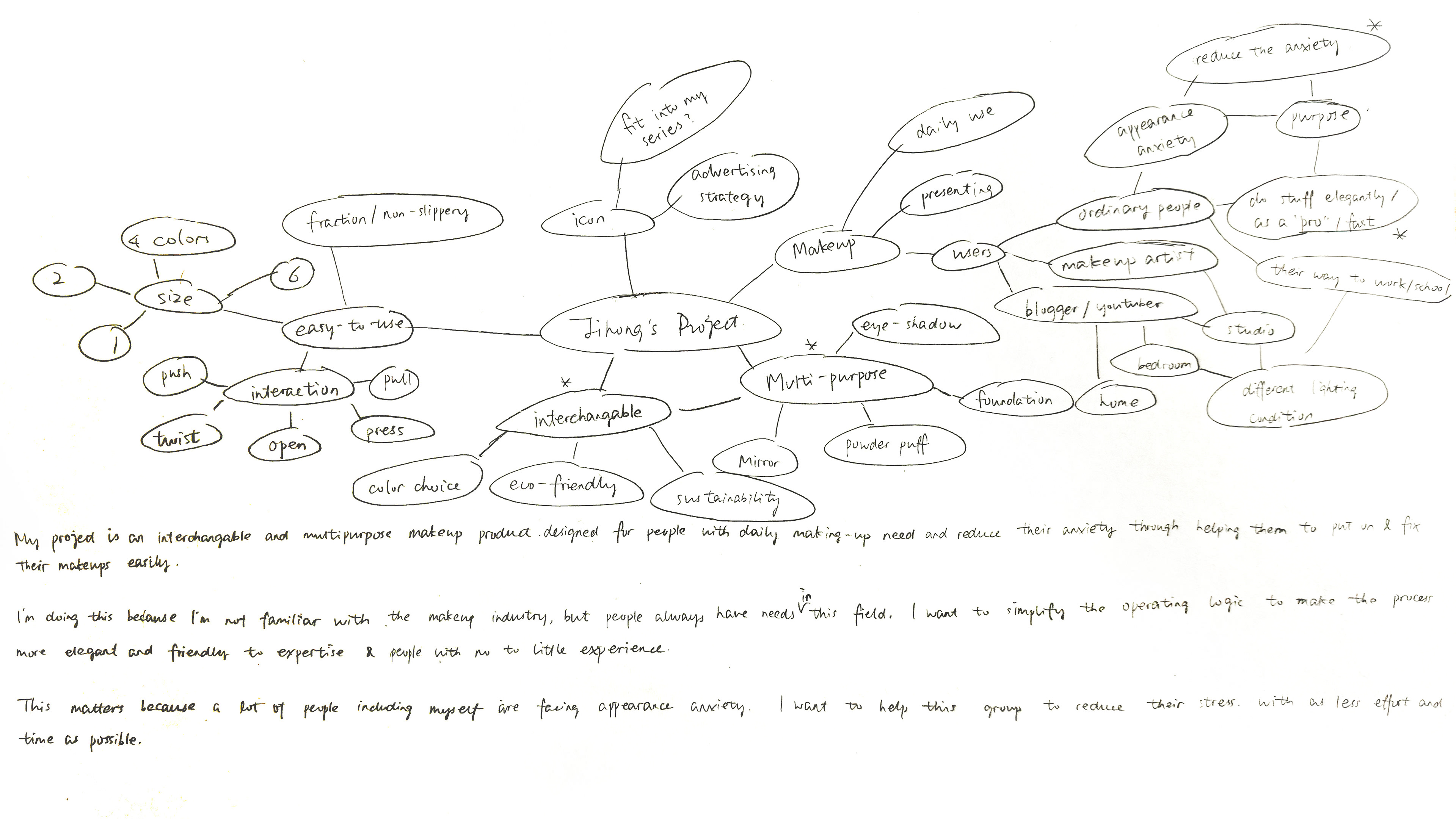
Research
The main beneficiaries of this product will be people with a certain level of makeup requirement but do not regard it as a career or profession. The easy-to-open box and multipurpose features could fulfill their daily requirements easily. Makeup artists could also benefit from this product, because the simple operation to open/close the box frees their hands, and the customizable palette gives them more freedom to create their own color combinations.
After comparing around 20 existing products in the market, I realized that the average number of colors (or cells) contained in an eyeshadow palette is 9, and the minimum number is 4. To make the product more friendly to beginners, I decided to stick to the minimum colors. Then I conducted a few rounds of basic user interviews and found out that a brush, mirror and/or a powder puff is desired in a set of convenient makeup tools. The cells that hold the powder should also be interchangeable, so when the users need refilling or want new colors, they won't have to dispose of the whole vessel.
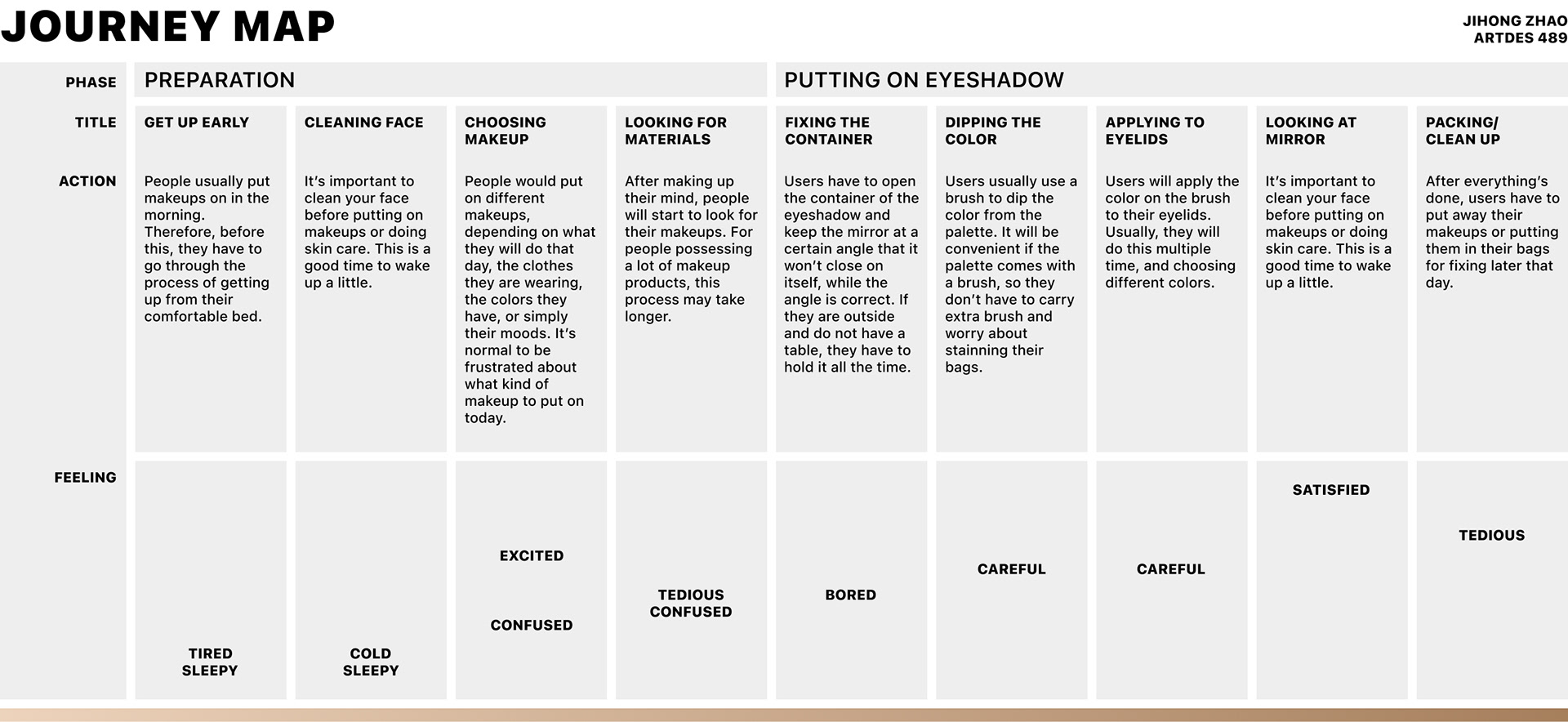
Ideation & Design
Inspired by the geometric expression of the Pythagorean theorem, I sketched a four-directional mechanical system driven by a gear in the center, which is connected to the cover and will be twisted by the users. The four "drawers" will slide along their tracks engraved on the base. Some non-slip strips will be pasted on the bottom surface so the vessel will be fixed in position when users are trying to twist it with one of their hands. I spent some time figuring out how to connect the gear and the cover while they spin around the base as a whole. I ended up with a structure that makes use of the elasticity of resin. The extruded structure connected to the base will stuck on the gear without touching the cover. Then I could glue the gear and the cover together (shown on the right).
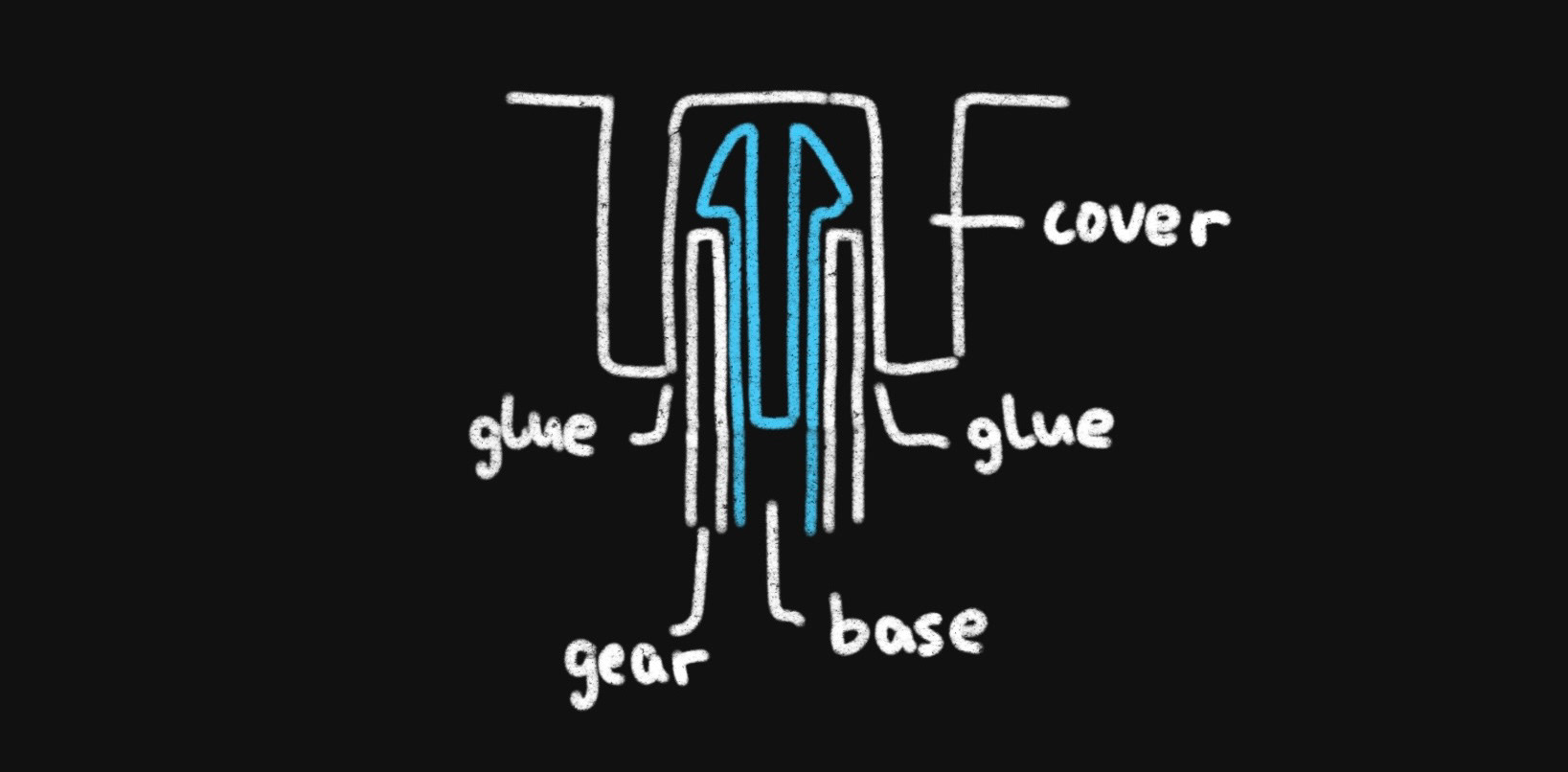
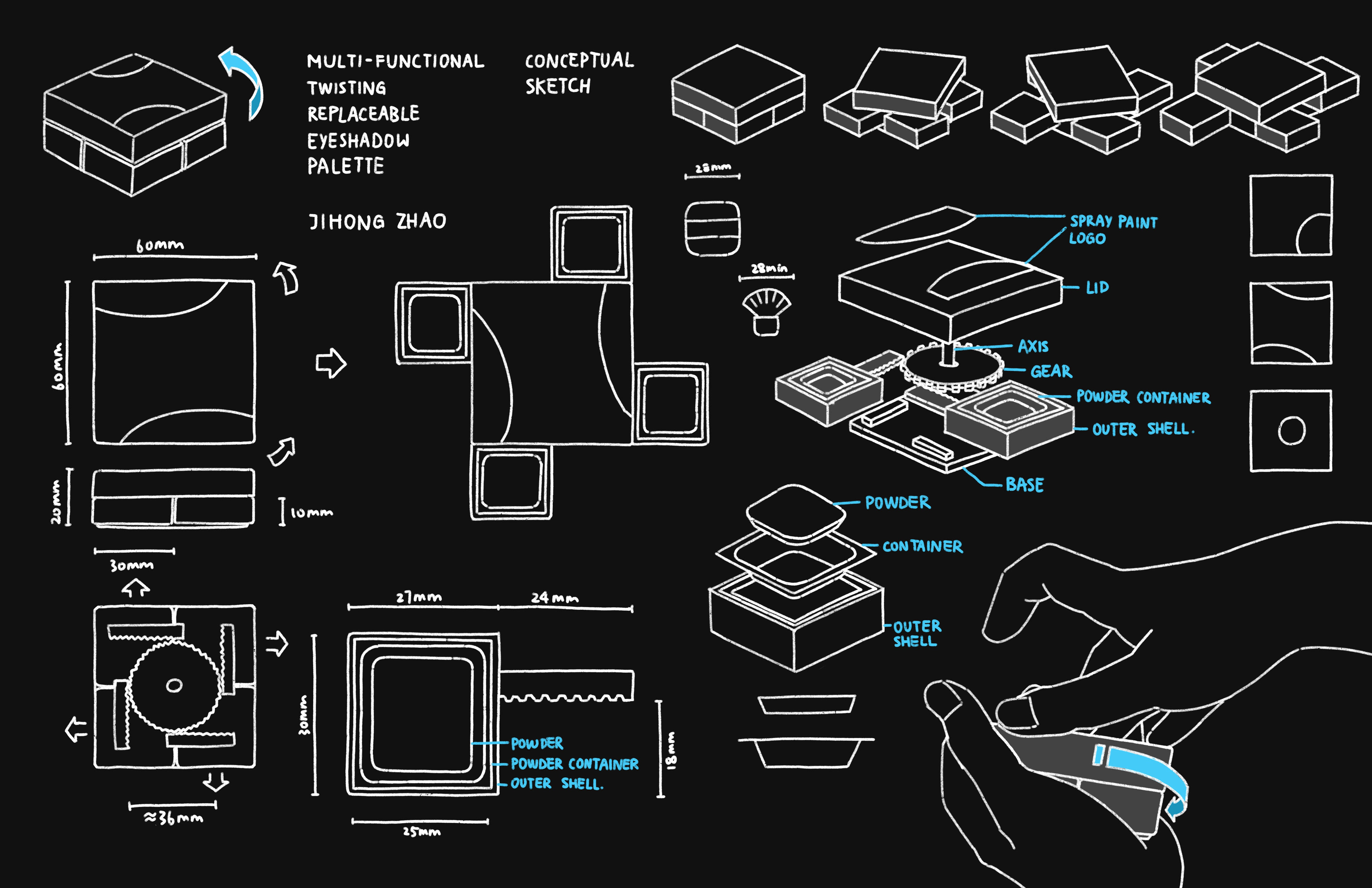
Concept Validation
I did another round of user interviews to test the validity of the concept by presenting them with the concept sketches. A potential core user mentioned that she meets the problems mentioned above sometimes during her make-up process, so these problems are worth solving. She also commented that the “twisting” does simplify the operation, and the non-slip strip on the bottom enables this operation. Another professional makeup artist pointed out that the cost of making such a vessel might be expensive.
I also tested the mechanism of the gear system through the physical simulation system in Blender. This model will also be used to print the components in further steps.
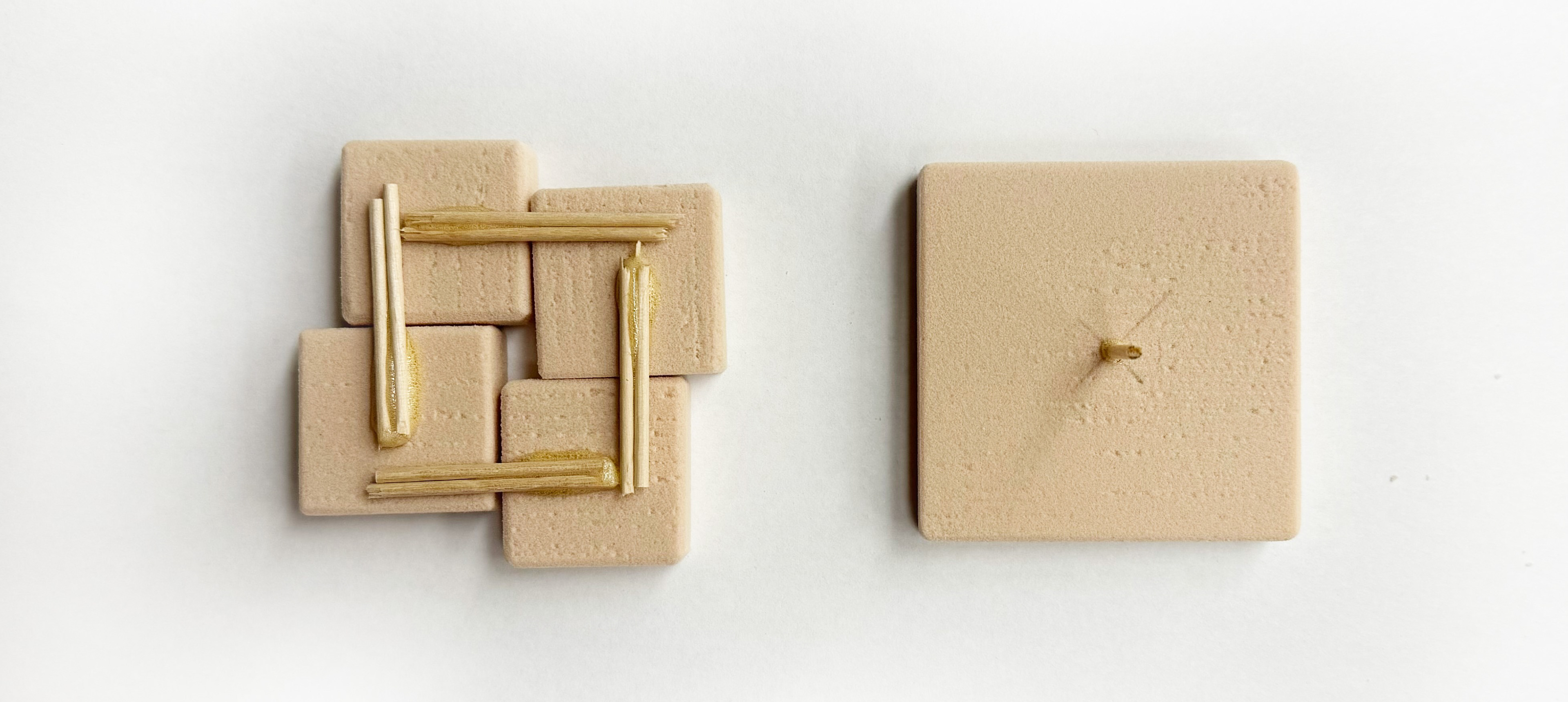
Prototyping
The first iteration of prototyping is made with toothpicks and model foam, mainly focusing on testing the dimensions of the product. The planned dimension was 60mm x 60mm x 20mm, and after the testing, it turned out that this was too small and couldn't hold enough powder. Therefore, I increased the dimensions to 75mm x 75mm x 30mm in the final model.
Then, I 3D printed the model built in Blender with clear resin. To reduce the cost in time and money, I only printed the essential components including the base, the gear, and one drawer to test whether the drawer could move along the track and whether the teeth of the gear worked with each other. It turned out that I didn't leave enough space between the track, so the drawer stuck in the track. I improved that in the second iteration.
When I was satisfied with the models, I sanded them and applied finishes. I applied a metallic finish to the cover so it works as a mirror and a clear finish to everything else so users could see the color inside.
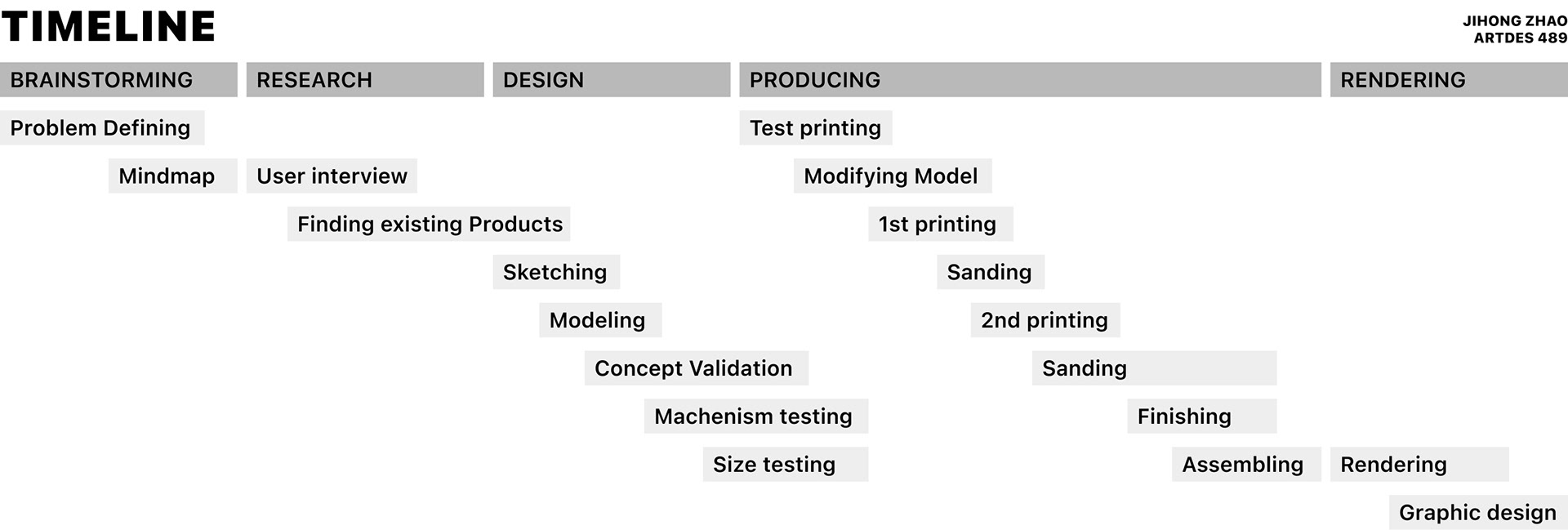
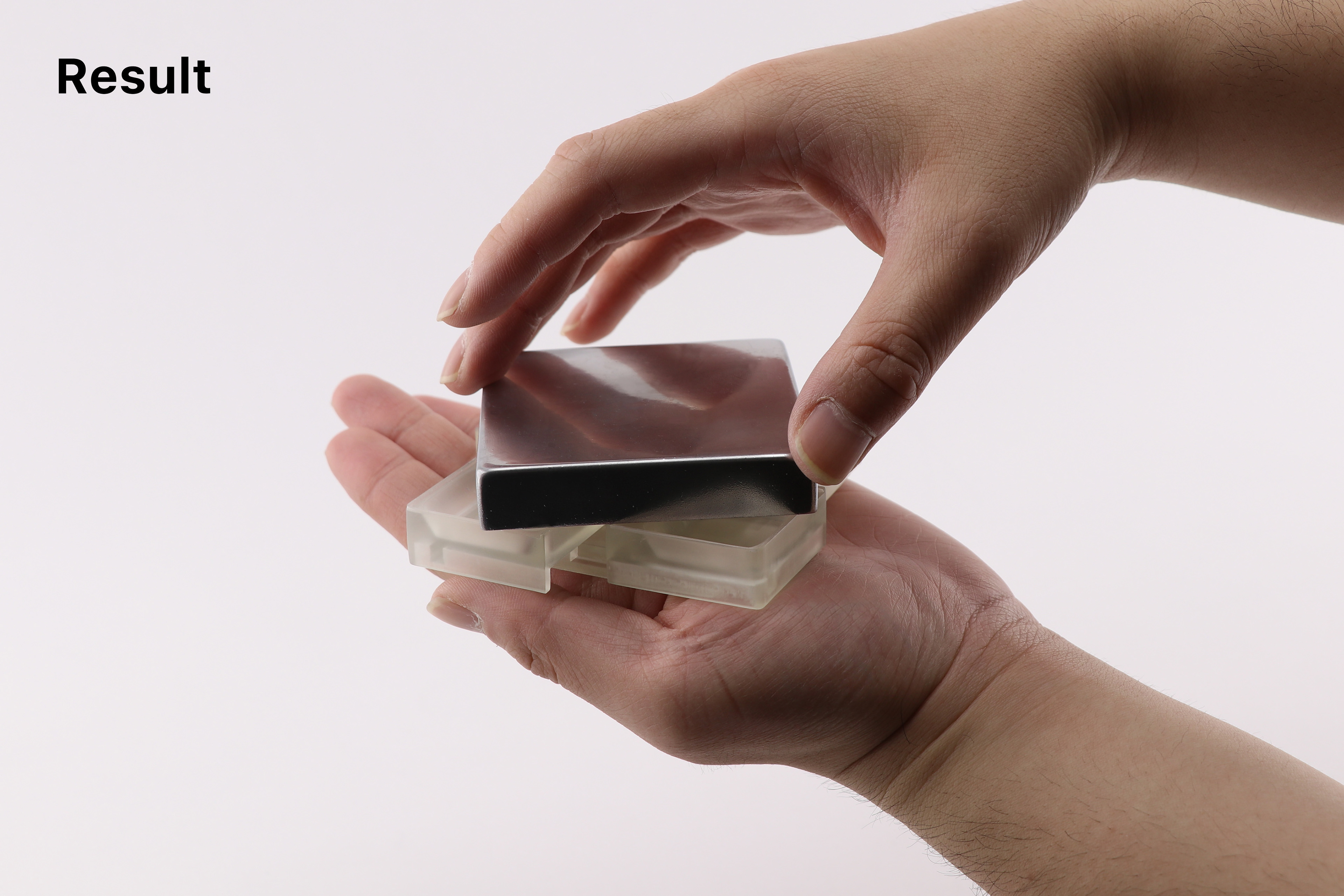
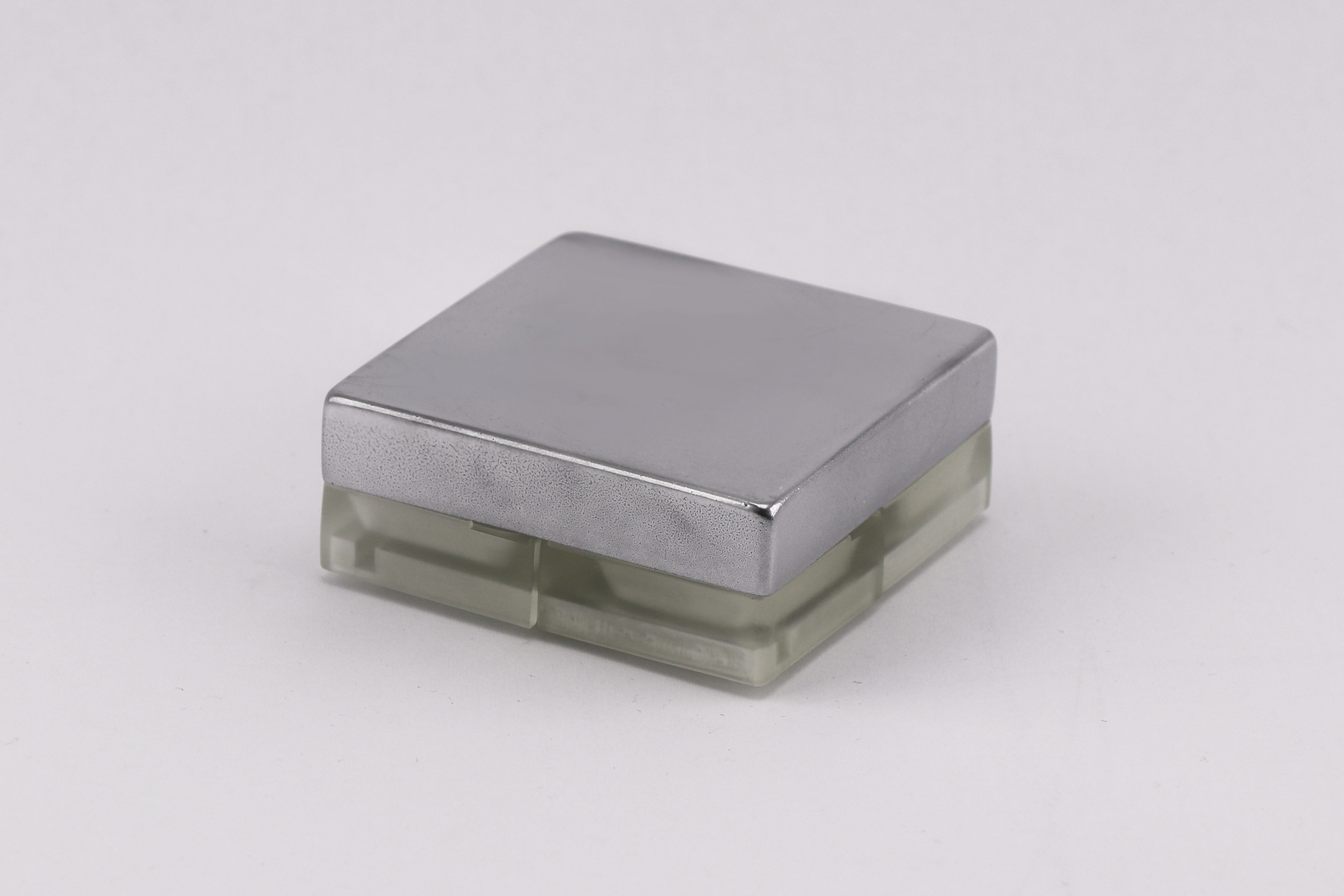
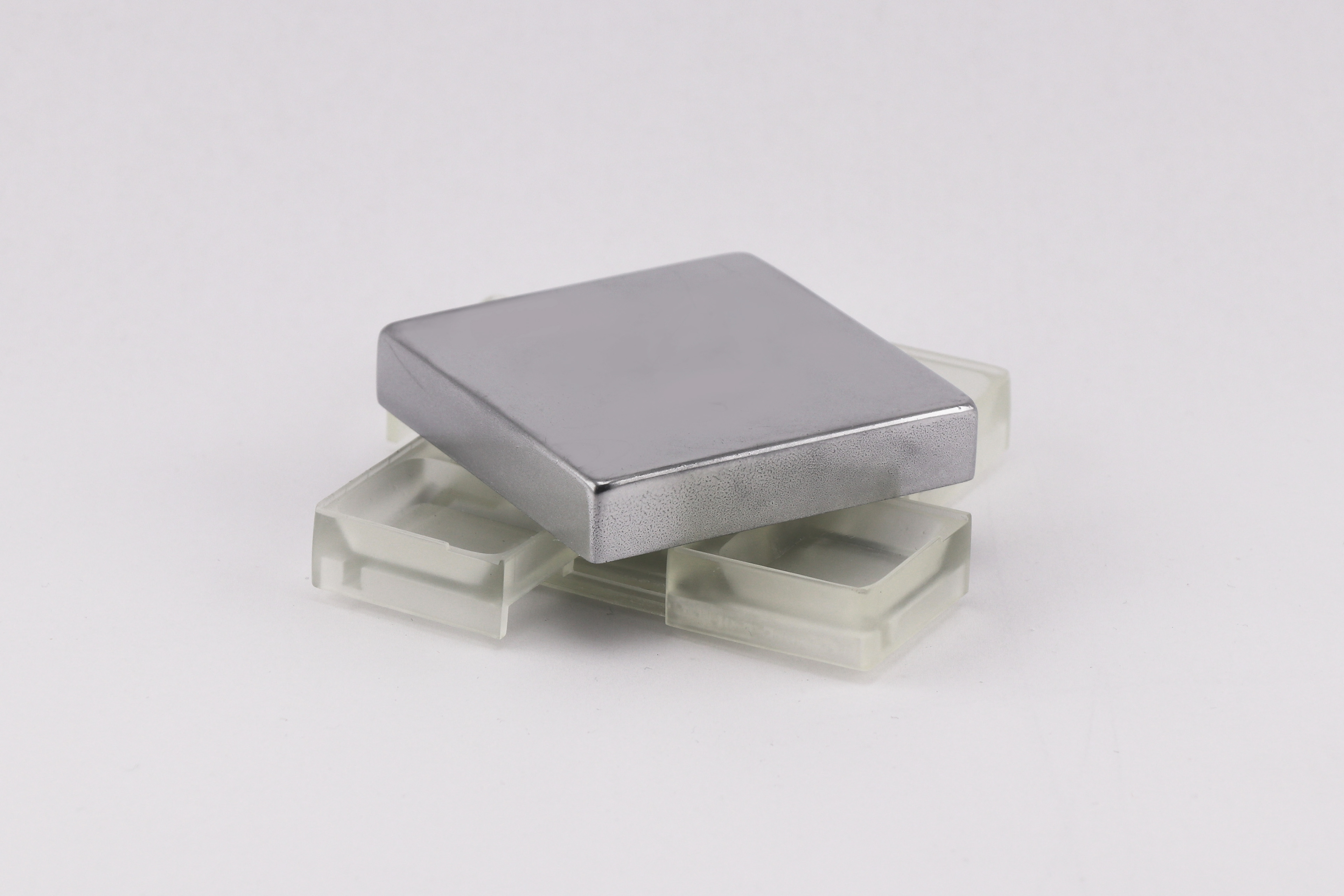
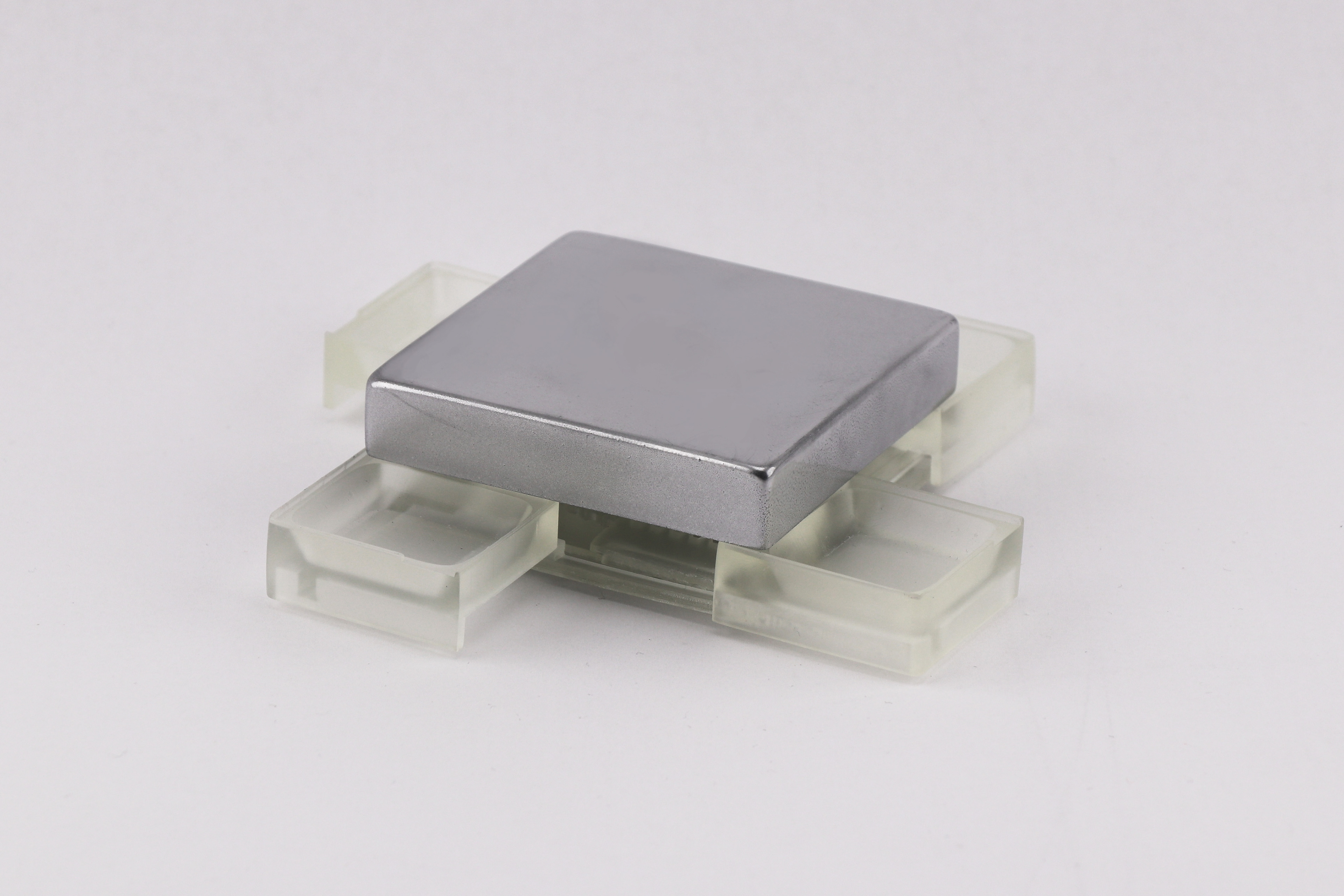
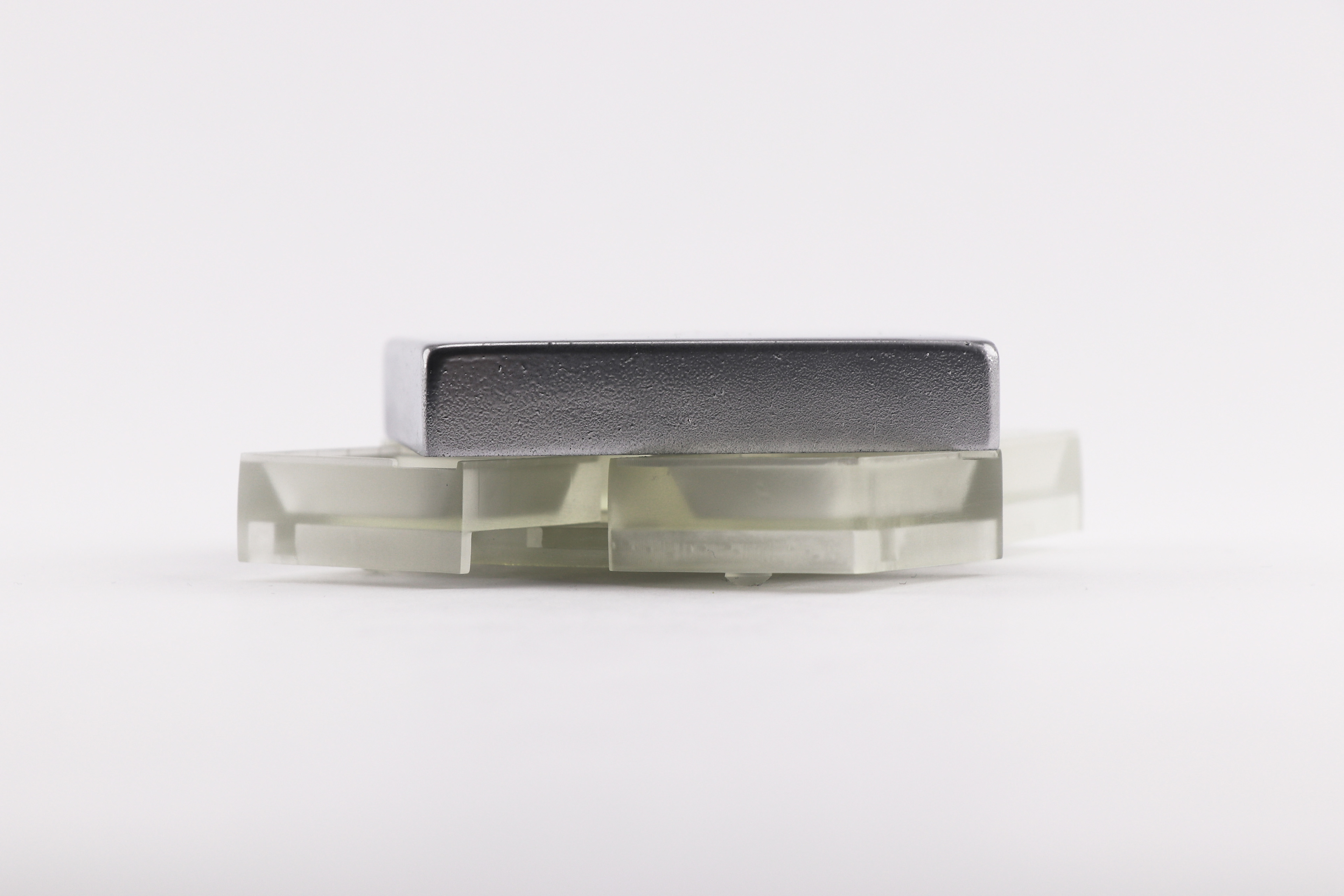
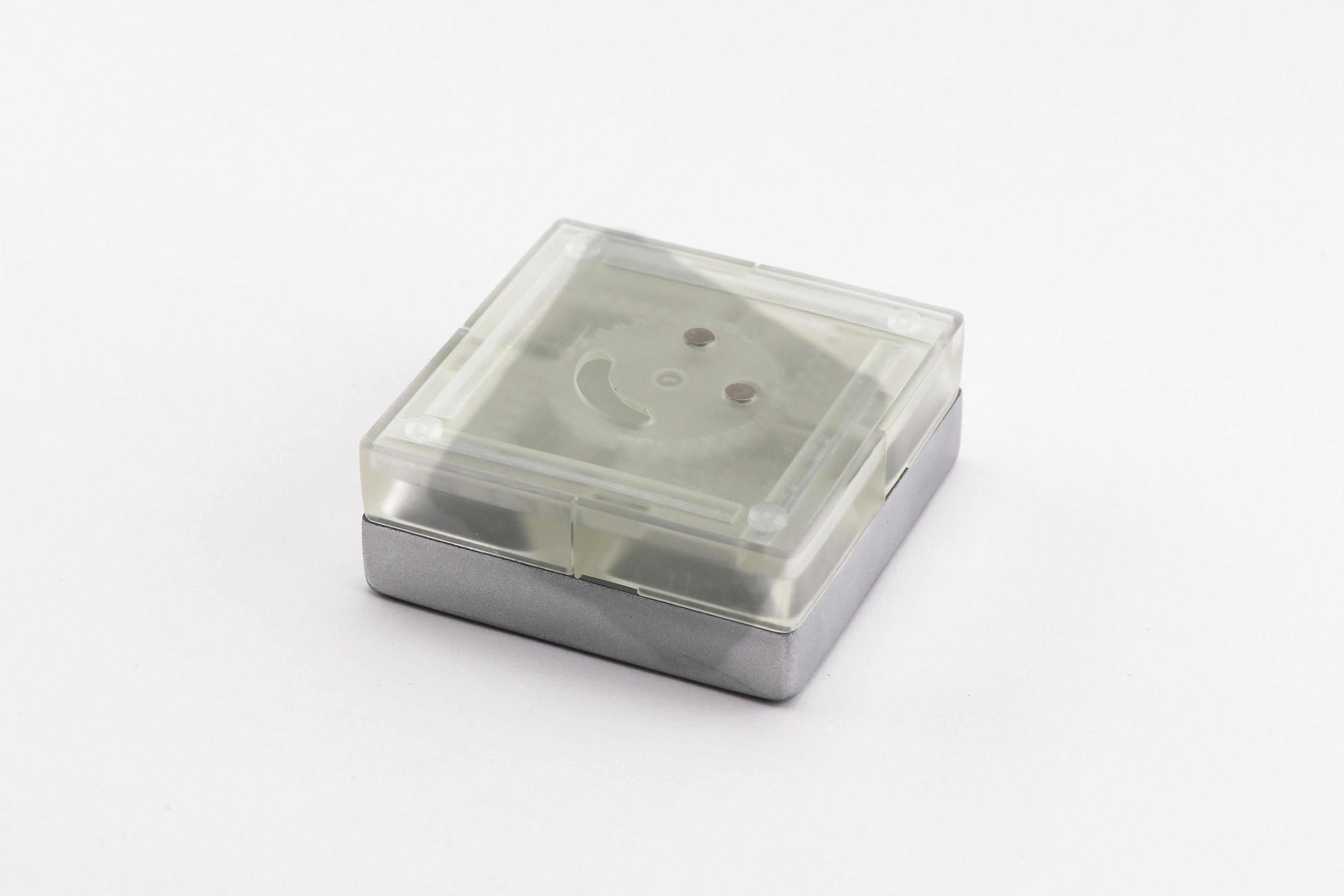
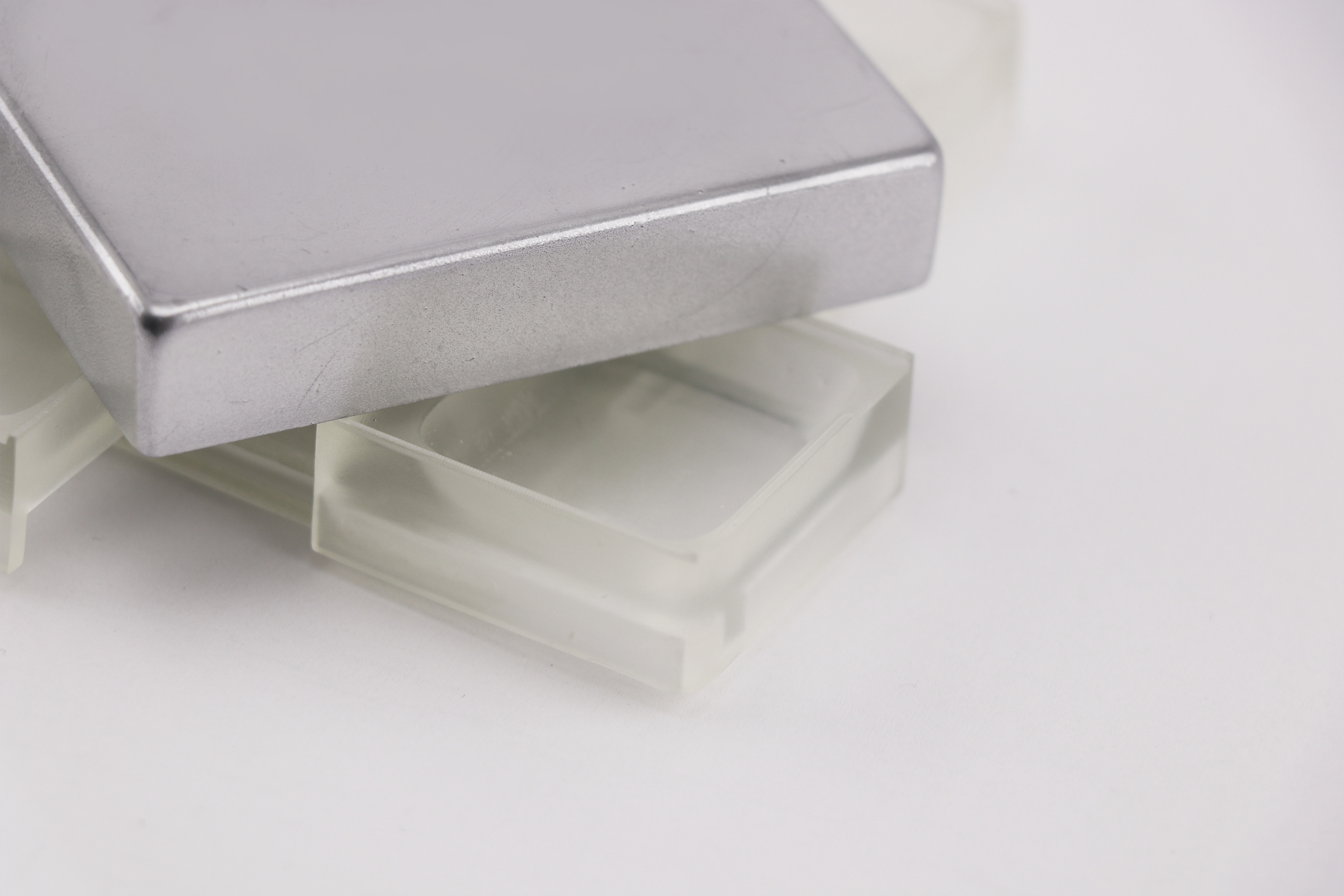
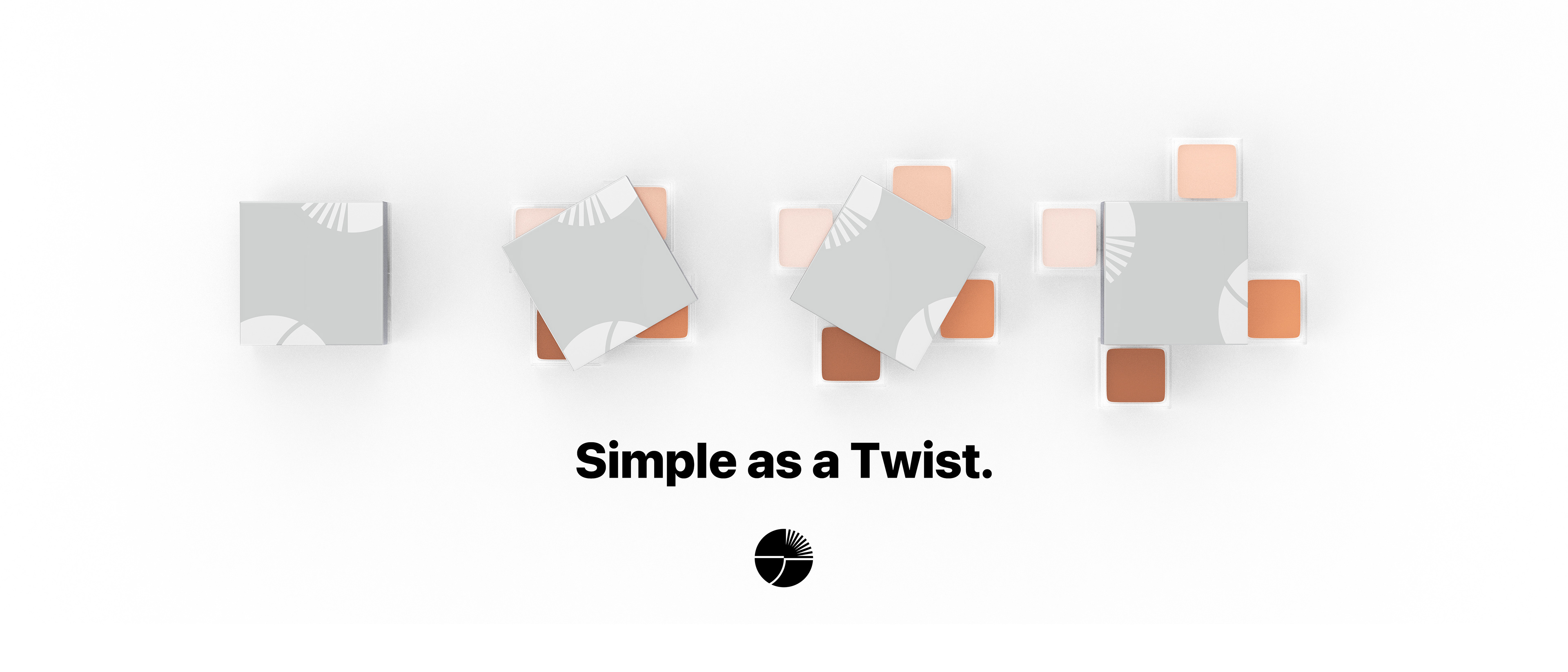